What is SCADA?
SCADA systems explained
What does SCADA stand for?
Supervisory Control and Data Acquisition (SCADA) systems are used for controlling, monitoring, and analyzing industrial devices and processes. The system consists of both software and hardware components and enables remote and on-site gathering of data from the industrial equipment. In that way, it allows companies to remotely manage industrial sites such as wind farms, because the company can access the turbine data and control them without being on site.Â
What is a SCADA system used for?
The main purpose of a SCADA system is to monitor and control equipment in industrial processes. Thus, SCADA systems are seen almost everywhere. Typically, SCADA systems are used in
Manufacturing
Water management
Oil and gas
Transportation
Renewable energy
Power distributions and control
In these industries, SCADA systems provide valuable information to key stakeholders. They can use the system to improve the performance of the industrial plants, keep track of the plants’ efficiency and mitigate errors and downtime through messages received from the system.
In today’s industrial advanced world, SCADA systems are crucial for operating industrial plants more efficiently, as they are much easier and faster in collecting essential data. This allows for better allocating of resources in many businesses.
A SCADA system connects to many different types of equipment. It monitors and controls everything from weather sensors and pumps to power production and motors, depending on what kind of data is needed.
How does a SCADA system work?
A SCADA system consists of three main system components. Combined, they ensure that data is transmitted from the equipment that needs to be monitored and controlled (sensors, motors, etc.) to an interface where the data can be analyzed and used for reporting.
The connecting link in the SCADA architecture are the Programable Logic Controllers (PLCs) or Remote Terminal Units (RTUs). These are microcomputers that interact with both the equipment (also called field devices) on the one hand, and HMIs, which are Human Machine Interfaces, on the other hand. HMIs are also referred to as graphical user interfaces.
As the illustration shows, the PLCs and RTUs works as local collection points that send and translates data to the remote or on-site HMI and send back control commands to the field devices.
The human operators access the data through the HMI, which can either be cloud-based or based on own servers. The software interprets and displays the data in an easy-to-understand matter, so operators quickly and simply can analyze and react to alarms.
Some SCADA systems also include options for automatic control actions and an automatic reporting engine for easy-made reports.
Alarms and events in SCADA systems
An example
Being able to react quickly to alarms and events can be vital for industrial plant operations. A typical scenario will be that the SCADA system notifies the plant operator in the HMI if something is not running correctly. Like a notification on your phone, the plant operator receives a message that he needs to react and assess the situation. If he makes the judgment that the equipment needs to be stopped, he can do that directly in the HMI, which sends commands to the PLCs or RTUs, which also sends through the commands and stops the equipment on site.
Due to the notification from the SCADA system, the operator can react quickly to emerging issues and prevent possible maintenance costs.
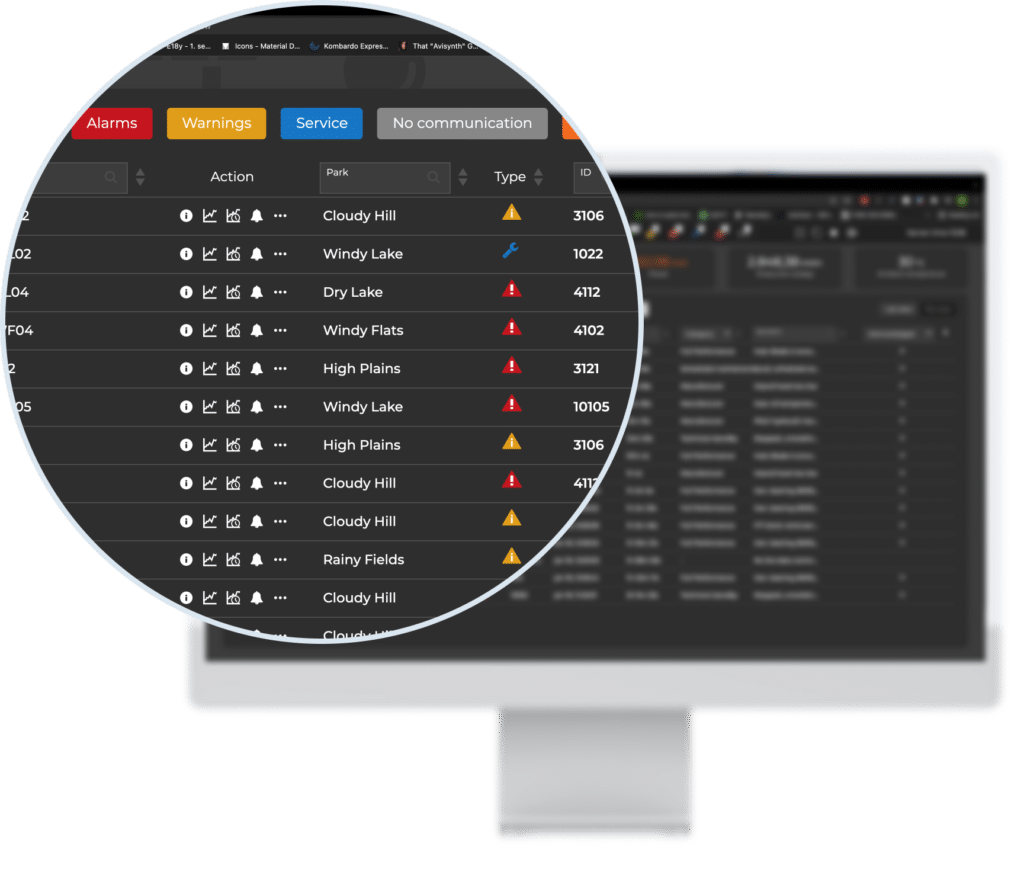
Why is a SCADA system important?
There are many benefits of a SCADA system. Overall, SCADA systems help optimize production and control the production according to regulations within the industry. In many cases, SCADA systems are also used for troubleshooting purposes, as maintenance has become a big part of securing a continuous production flow without too many errors.
To fully understand the importance of a SCADA system, we need to go back to when industrial plants were monitored manually and relied on personnel to be on site during production. The personnel had to oversee and control operations and react to emerging issues. This was not only costly but could be dangerous for the personnel.
However, as industrial sites scaled up and became more remote, the need for more automatic solutions came about.
Fast forward to today, the initial need for more automation is still driving the SCADA development. With more automatic and semi-automatic processes, businesses can allocate their resources differently and save money in the long run.
What kind of data does a SCADA system collect?
A SCADA system can collect any type of data from plant equipment, such as temperature, pressure, and speed data, as long as there is a connection to the equipment. Data from the equipment is the raw data that the PLCs or RTUs then translate into comprehensible information for human operators to act upon.
What is very useful is that a SCADA system typically collects both live and historical data. Live data is often used for maintenance purposes as well as real-time tracking. On the other hand, historical data is often used for reporting and to improve plants’ performance.
The monitored equipment doesn’t have to be from the same vendor in order for the SCADA system to transform the data into understandable information. The equipment just needs to have an accessible communication protocol that the PLCs or RTUs can utilize. This opens up for uniform information exchange across plants.
In the wind sector, the IEC 61400-25 is the international standard for communications for monitoring and control of wind power plants. The standard enables the exchange of data and information with different wind power plants independently of a vendor.
Did you know?
Based on the IEC 61400-25 standard, SCADA International has developed the Global Wind Data Tag-List that transforms raw data into smart data by providing a streamlined naming convention for wind turbines. It comprises a vast range of 2600+ tag-names and data points covering diverse wind turbine types, models, and brands.
Why are SCADA systems used in the renewable energy sector?
SCADA systems are today used at any wind power plant as they allow for remote monitoring and control of the wind turbines. As wind power plants or wind farms have grown in size, it is no longer possible or favorable to visit every wind turbine to collect data for monitoring and control purposes.
You can use SCADA systems in wind parks
You can use SCADA systems in solar PV plants
You can use SCADA systems in hydropower plants
Offshore wind parks are also on the rise these years, which means remote access to the wind turbines becomes even more crucial. With a SCADA system, a lot of tasks can be performed without even visiting the wind turbine.
Other renewable power plants such as solar PV (Photovoltaic) or hydropower plants also rely on SCADA systems to gain remote access and control. These plants are often placed in remote areas, where it is both difficult and costly to bring personnel on site.
Another reason why SCADA systems are so essential in the renewable energy sector is that SCADA systems enable monitoring and control of the power production and power production loss. The demand for electricity from renewable power plants is growing day by day as the industry moves away from harnessing energy from fossil fuels to more green alternatives.
The renewable plant owners are thus looking to optimize their power production as much as possible. Detecting any errors or under-performance quickly and effectively can be a way to reduce downtime of, e.g., wind turbines and optimize the overall performance of the power plant. Controlling the power output is also an effective way to comply with grid regulations and optimize the plant’s performance.
How can SCADA International help me?
SCADA International delivers solutions for the complete SCADA value chain. We operate in the renewable energy sector and have installed numerous SCADA systems for big players within the wind, solar PV, and hydropower industry, respectively.
As our name reveals, we specialize in SCADA systems, and our team consists of SCADA experts covering everything from engineering and design, installation and commissioning to service, surveillance, and consulting. We strive to reduce complexity by providing our customers with SCADA expertise and cutting-edge solutions.
With more than 6000 SCADA solutions installed across 29 different countries worldwide, SCADA International has vast experience in the field of monitoring, analysis, and control.
The OneView® SCADA is our future-proofed SCADA software that empowers the renewable energy sector. The system lets you monitor and control all your renewable assets – e.g., wind turbines or solar PV modules – in one single view. In that way, you don’t have to log in to several different systems in order to keep on track with your different assets. Thus, asset management becomes a much easier task, and you can mitigate problems much quicker.
Did you know?
SCADA International also has vast experience in developing new drivers for both standard and OEM-specific protocols. Many OEMs (Original Equipment Manufacturers) use their own protocols (communication rules). These rules can make it difficult to interface to various controllers and other devices from the OEMs. In order to understand the protocols, SCADA International has, over time, built competencies in developing drivers so the OneView® SCADA system can communicate via many different protocols. This is beneficial for the customers, as they get a system that is compatible with many different OEM systems.
Many businesses choose OneView® SCADA because they get:
- Control of all assets at all levels
- Ownership of your system and data
- Analysis and monitoring in one system across asset types and manufacturer brand
- Joint reporting across technologies
- Reduced data and system complexity
- Optimized performance and diagnostics
- Access to 24/7/365 SCADA expertise and support